随着精密机械制造、航天、国防等工业的发展,特别是近年来对零件性能、精度要求的提高,使真空炉的准确控制越来越受到人们的重视。真空气相回流焊是一种高精度、高可靠性的电子元器件焊接技术,它通过在真空环境下利用气相化学反应将焊锡膏转变为液相,并将其应用于电子组装中。
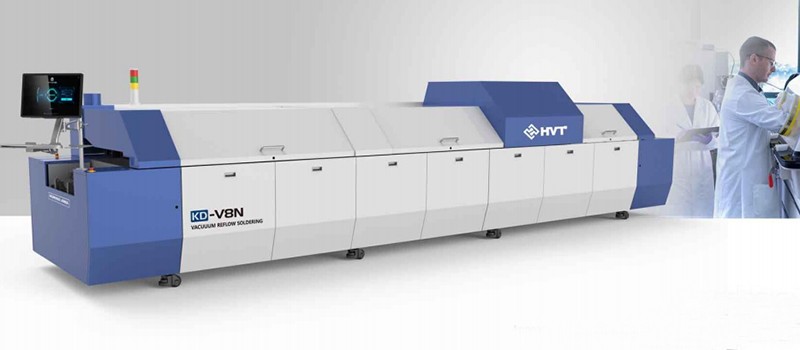
一、工作原理
焊接前准备:将需要焊接的电子元器件和基板放置在真空炉中,然后在焊接区域上涂布焊锡膏。
抽真空:开始抽真空,将炉腔内的气体排除,真空环境下的焊接可以有效避免氧化反应的发生,并提高焊接质量。
加热升温:设定所需的加热速率和焊接温度,并开始加热。通过加热,焊锡膏中的活性助焊剂会在真空环境下蒸发形成气相,然后在元器件表面和基板焊盘上进行化学反应。
液相焊接:当达到焊接温度后,焊锡膏在元器件和基板上形成液相。由于真空环境下的低压作用,液相焊料会均匀地覆盖在焊盘上,并且无气泡和虚焊现象。
冷却降温:在焊接完成后,停止加热并开始冷却,通过控制冷却速率,可以避免焊接过程中产生应力,从而提高焊接质量。
压力释放:当炉腔温度降至安全范围后,打开炉门,释放压力,并将焊接好的电子组件取出。
二、特点
高精度:真空环境下进行焊接,可以有效避免氧化反应和焊接表面污染,提高焊接质量和可靠性。同时,真空环境下的焊接可以实现较小的焊盘间距和焊锡膏量,适用于高密度电子组装。
无气泡和虚焊:由于真空环境下的低压作用,焊锡膏能够均匀地覆盖在焊盘上,避免气泡和虚焊的产生。这样可以提高焊接质量,并减少后续测试和修复工作。
温度控制准确:具备准确的温度控制系统,能够根据需要设定和维持所需的焊接温度,温度控制的准确性对于焊接质量和组件可靠性至关重要。
适用范围广:适用于各种电子元器件的焊接,包括BGA(球栅阵列)、CSP(芯片级封装)和QFN(无引脚封装)等,它适用于不同尺寸和形状的元器件,满足多样化的焊接需求。
环保节能:采用真空环境和低温焊接技术,相对于传统的浸泡焊接或热风炉焊接,能够减少焊接过程中的能耗和废气排放。
真空气相回流焊能够实现高密度封装技术,满足先进电子产品对小型化和轻量化的要求,广泛应用于电子制造业中,特别是对焊接质量和可靠性要求较高的领域,如航空航天、汽车电子、通信设备和医疗器械等,在高密度封装、高可靠性焊接、微观焊接和无铅焊接等领域具有重要的应用价值。